THE NOVIQU BLOG
Four Principles for Keeping your Warehouse Clean and Organized
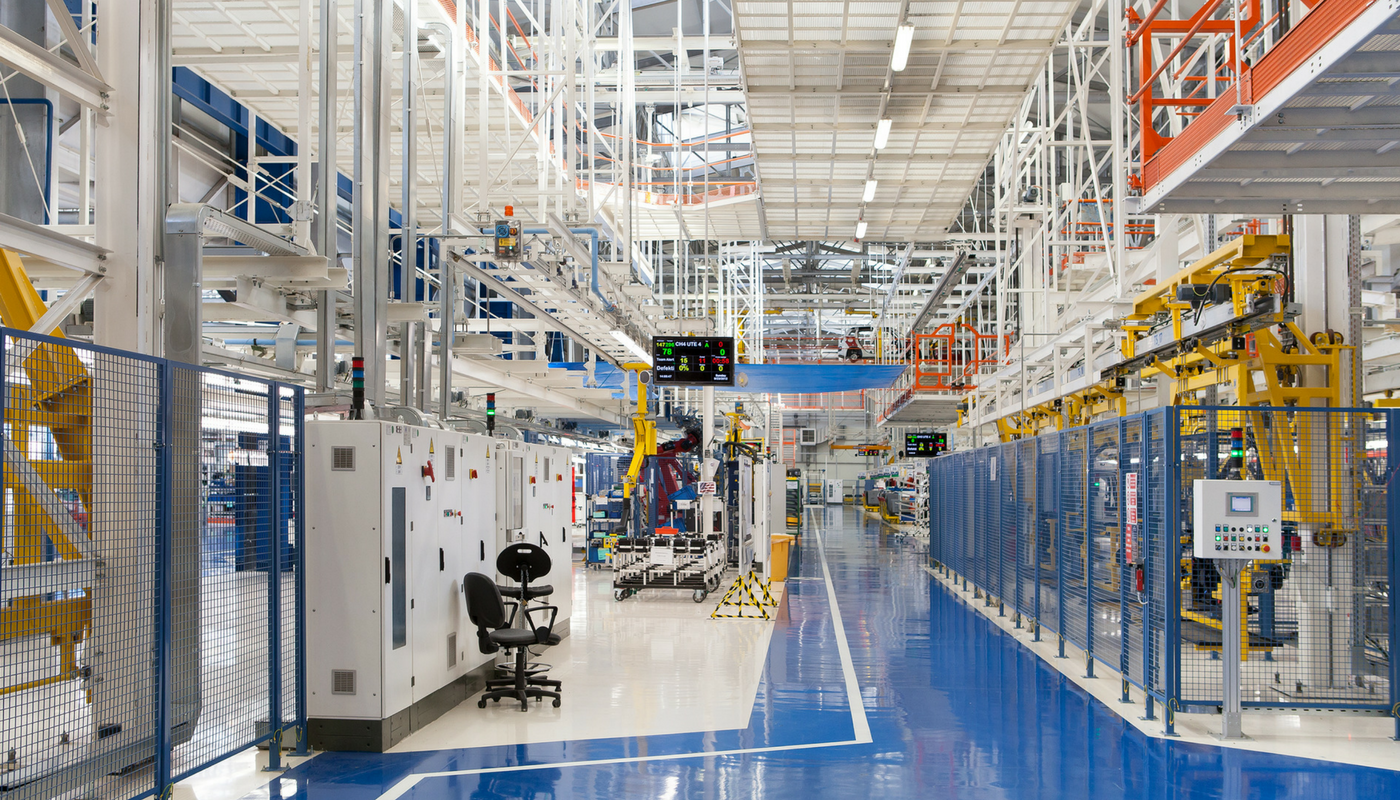
It should go without saying that a disorganized warehouse can and may eventually lead to all sorts of accidents down the line. Before that happens, employees have to work less efficiently in an environment that promotes low morale. Likewise, dirt and grime can cause machinery and other equipment to malfunction earlier, leading to further costs and unexpected delays in the production process. Negligently stored pallets and plastic wraps can pose a trip hazard or may act as extra obstacles for forklifts to maneuver around.
These are just a few examples of what a disorganized warehouse has to offer. Sometimes it may seem overwhelming to take the time to organize and clean your warehouse space – but the up-front work can reap benefits in the end. Below are four reasons to keep that warehouse clean and organized.
Ergonomic Safety
="http://www.cisco-eagle.com/blog/2015/04/02/ergonomic-safety-tips-for-the-warehouse/" target="_blank">Ergonomic equipment is a worthwhile investment; not only will it keep your employees safe from certain accidents but it also allows them to work better and more efficiently. This investment will keep the company away from any potential liabilities down the road. To determine where you may need this sort of equipment, walk the warehouse floor and look for signs of awkward posture and repetitive motions in the form of reaching, carrying, or lifting, heavy-duty lifting and manipulating, and so forth. And there’s always the good old fashioned method of talking to the employees to see what their input is on the matter and what equipment would make them happy.
The Pareto Principle and ABC Analysis
The Pareto Principle, or more commonly known as the 80/20 rule, can be found everywhere in nature and can be applied equally as well in warehousing. In short, this principle implies that 20% of causes generate 80% of results. In other words, 80% of revenue will come from just 20% of products, which we usually call top sellers. The ABC analysis is an inventory optimization method that utilizes the Pareto Principle by categorizing items in their order of importance. Figure out what products are your top sellers and store them close to the loading dock to provide faster shipping and less manipulation around the warehouse.
The 5S Methodology
Developed during the 16th century in Japan, the 5S methodology is used by many companies around the world as a means to make the workspace safer and more efficient. Sort all the items in your inventory and throw out any unnecessary clutter. Straighten everything up for easy tracking and access. Bring everything to a shine. Standardize this practice among the entire staff so that it becomes second nature. Work to sustain everything that's been said here.
The 3R Methodology
If the above mentioned, 5S seems too challenging to implement in your organization, then consider the 3Rs - reduce, reuse, and recycle. Like 5S, you start by reducing the amount of clutter or unnecessary tools or materials that are lying around the warehouse collecting dust. Reuse anything that can be reused, such as the pallets. Statistics show that over half of all pallets are thrown away after only one use. Instead of just throwing stuff away, consider recycling them. Most materials such as wood, metals, plastics, and glass can be recycled, and you'll be doing both your business and the environment a favor. Plus, it will give your staff a deeper sense of accomplishment.
Keeping a well-organized warehouse may seem like a daunting task – but it doesn’t have to be. With a simple dose of perseverance and an end goal in mind, your storehouse could be performing at top efficiency in no time.
More
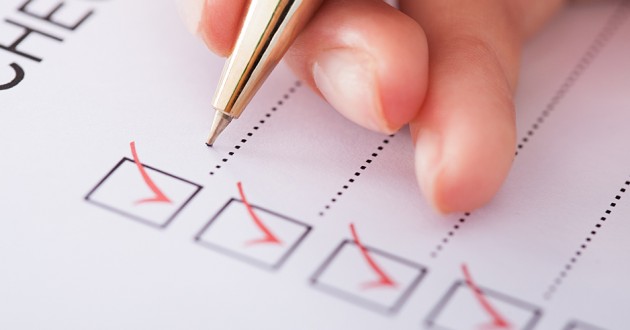
Posted on 06/06/2018 by Anna Haney
The Importance of Digital Checklists

Posted on 11/2/2017 by Chad Haney
The Future of the Manufacturing Industry
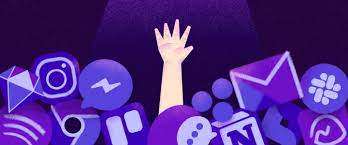
Posted on 03/22/2022 by Anna Haney