THE NOVIQU BLOG
Industry 4.0: What it is, and how to begin implentation now
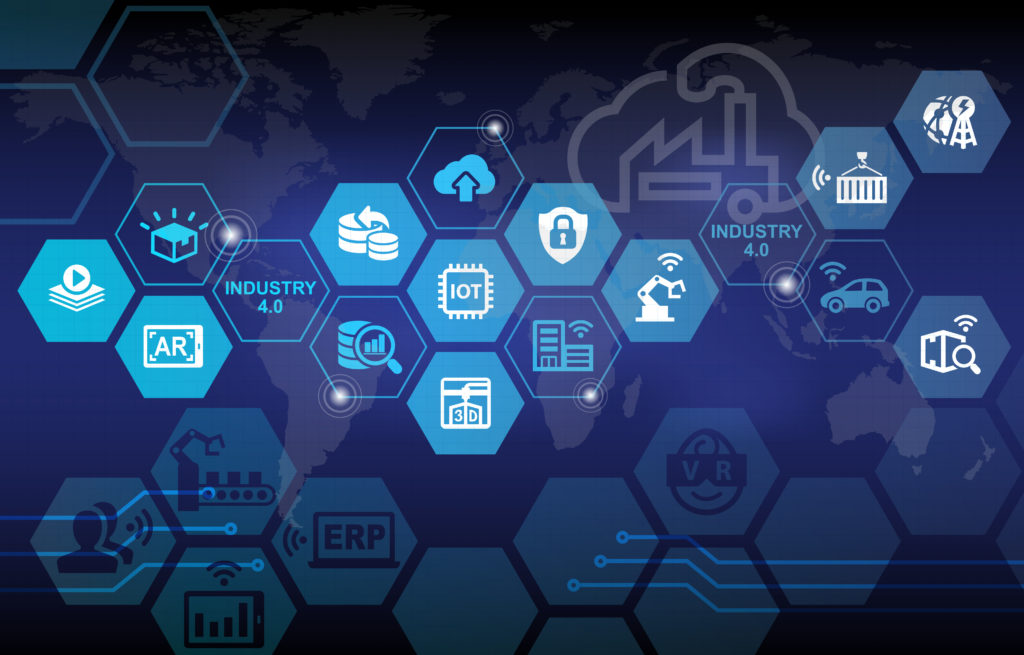
“The fourth industrial revolution” – Industry 4.0 for short – is a global movement in manufacturing that started in Germany in 2012. It’s been a few years since it began, but there’s still a fair amount of confusion around the subject, what it means for American manufacturing, and why people should care.
What is Industry 4.0?
The movement has evolved over time but made its beginning by trying to incorporate computerization and digitization into manufacturing processes. The first industrial revolution focused on mechanization, the second on mass production/assembly lines, and the third included more automation, this fourth revolution aims to make process more connected, more knowledgeable, and technically sound (and safe – but more on that in a bit). Below are the four core principals of Industry 4.0.
Interoperability
This mouthful of a word really boils down to one simple thought: computer systems and software need to be able to trade and make use of information. Bottle filling machines counting parts per hour need to talk to palletizers that know how many pallets of that same product are being shipped without delay. When systems become truly interoperable, facility managers can start looking at their facilities in ways they never have before. More data = more information, and more information means better decision-making capabilities.
Information Transparency
For us to be truly interoperable, there needs to be full transparency of information. To do this, virtual networks need to be able to create a digital copy of any physical asset. This is also sometimes referred to as a “digital twin.”
Having a digital twin means looking at any physical asset – such as a jet engine – without having to dissemble the actual component. You can look into and diagnosis issues from a virtual perspective, making the physical repairs, or tweaks, easier to get right on the first try.
Technical Assistance
This principal comes in two parts. First, the ability of digital systems to compile and visualize information that is gathered that enhances a human’s ability to do their job. Having a machine that can alert you by aggregating data that it thinks a ball-bearing will fail within the next 24 hours will allow you to set the repair on your own schedule, and not run your machines until fault.
Second, this brings together cyber-physical-systems such as robots, to do tasks that are unpleasant, exhausting or unsafe for humans. This creates safer environments for our employees and frees them up to do what humans do best – problem solve.
Decentralized Decision Making
Along the lines of human brains being used to problem solve, Industry 4.0 comes with an idea that we need to provide basic decision-making capabilities to our robotics systems. If we can allow our cyber-physical-systems to make simple decisions and continue running, we can see more efficient processes begin to appear.
How to Adopt Industry 4.0
Now that we know a bit more about what Industry 4.0 is, we can talk about what that means for American manufacturers, and how we can go about making small changes to adopt Industry 4.0 into our facilities.
Concerns: Terminator and Skynet
With any change in an industry there are always concerns with adoption, and Industry 4.0 is no different. Many concerns with the movement revolve around two core thoughts: humans and data security.
With the introduction of cyber-physical-systems, some are concerned that the robots will begin to steal all of the hardworking American jobs. While the smart-manufacturing sector is projected to be nearly $400 billion in 2025, many argue that industrial robots are actually a positive to the industry. By implementing robots into our facilities, we aren’t replacing human jobs – we’re making them safer, more efficient, and leaving the brunt work to a machine.
Concerns: Data Security
Another common concern with Industry 4.0 is the idea of data security. Currently, many smaller manufacturers have no in-house IT department, and the larger facilities have smaller groups that manage all of their internal resources. These professional’s entire job rests upon the security of the data in the facility, and keeping a closed system is the way to go.
While we can’t deny that that would work to some extent, with a shift towards more interoperability and openness in data communication, it’s just not a viable solution for the long hall. By training our IT professionals to understand and implement best practices in this ever growing digital world, manufacturers can have a better handle on their security, and thus their data.
Baby Steps towards Adoption
Change may not be the most welcome thing, but making baby steps towards Industry 4.0 adoption doesn’t have to be rocket science. There are many tweaks and small changes that can be made in facilities today to move the needle and get your facility closer to adoption.
- When replacing machinery, replace it with “smart” machines or devices. Anything that is already connected to the internet, or includes the ability to monitor it’s functions will be a great way to start integrating more data into your facility.
- Train your employees on how to adapt and welcome change. There’s a lot of change coming and if we don’t prepare ourselves and our employees, it leads to a rift later on down the road. If we can welcome change, and take suggestions for change from our employees, it will make shifts easier down the road.
- Partner with service providers. If you’re unsure of where to start, find a consultant or expert in the area you need help with, and gain insight through partnerships.
- Start tracking things digitally. Begin making the shift now to take any paper-process and make it digital. The more you can begin to utilize cloud based systems – such as Noviqu – the more interconnected your facility can truly be.
Industry 4.0 is just the beginning of a wealth of change coming to manufacturing over the next few decades. Industry 5.0 isn’t too far behind, and with the rate at which technology changes, we need to begin adapting now. Hopefully taking small steps today will move manufacturing towards large leaps in the coming years and help take all of us to the next level.
More
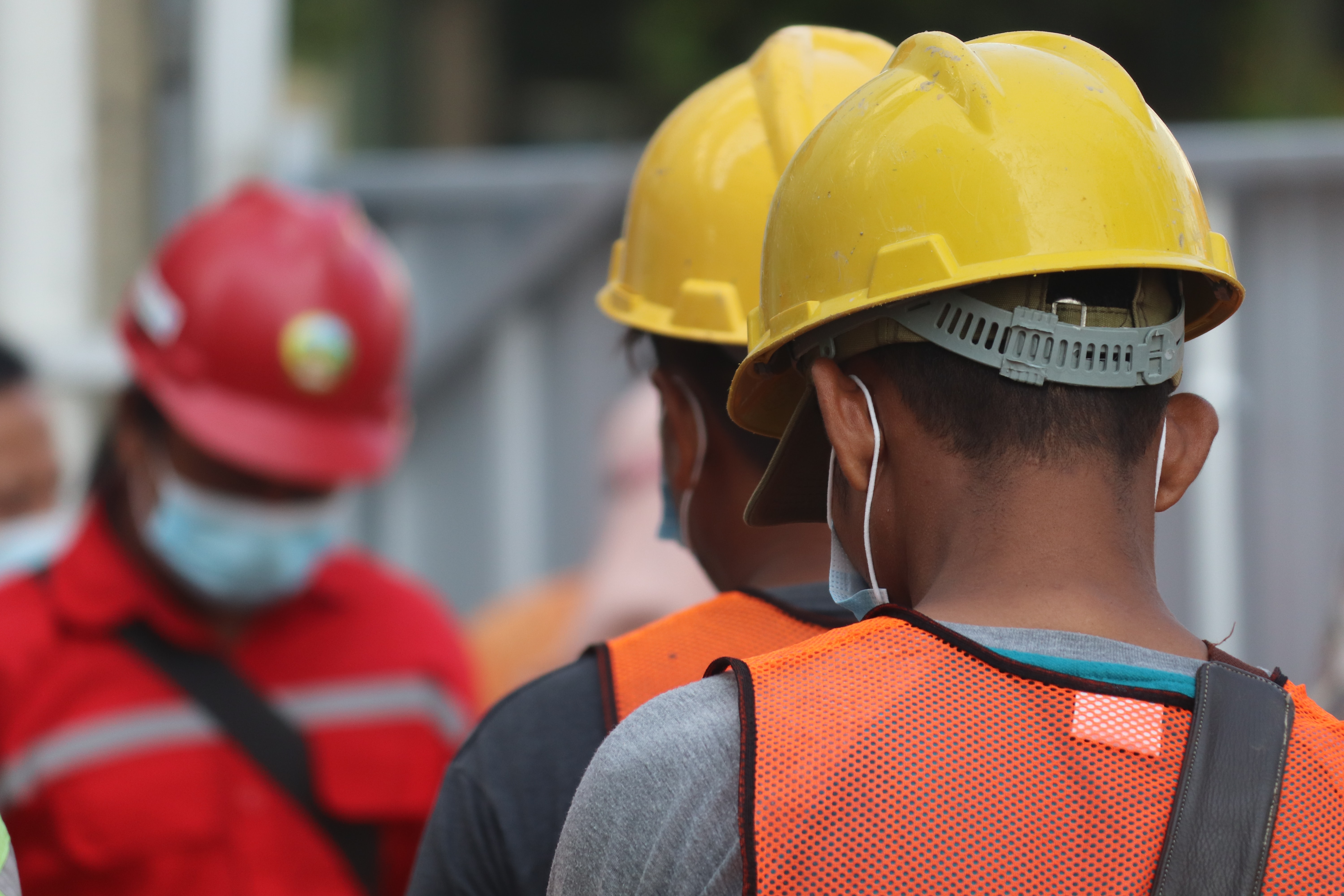
Posted on 03/16/2022 by Anna Haney
Three Steps to Build a Culture Focused on Safety
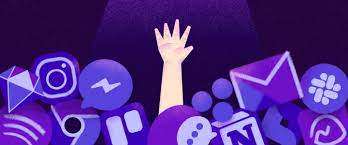
Posted on 03/22/2022 by Anna Haney
Information Fatigue- The problem with apps
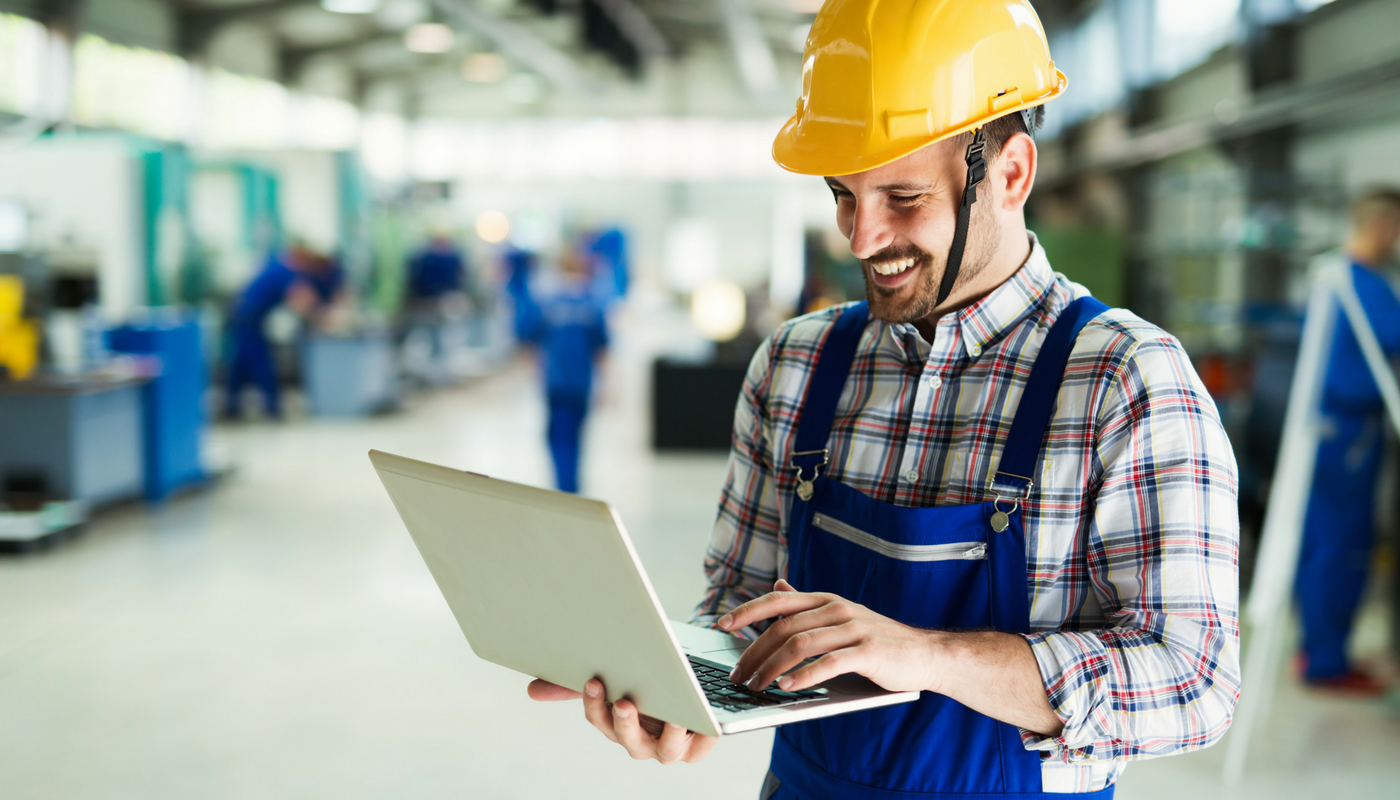
Posted on 03/27/2018