THE NOVIQU BLOG
3 Steps to a preventive maintenance plan employees will actually follow
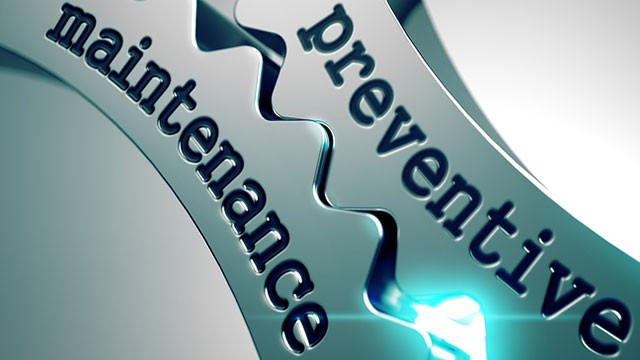
Does your facility have a preventive maintenance program in place? Preventive maintenance keeps equipment running smoothly and avoids costly maintenance issues or worse, the unspeakable shutdown.
Many workers don’t have the time or see the value in preventive maintenance and often skip it. Instituting an effective, easy-to-follow preventive maintenance plan will keep equipment running at peak performance, keeping your facility running smoothly.
Below are three ways you can put a preventive maintenance plan in place that employees will actually follow.
Make it clear and simple to follow
When instituting a new plan or raising awareness of an existing one, management must make the plan crystal clear. That could mean posting reminders next to equipment, pop-ups on digital machines at end of day, or incorporating it into the daily equipment checklist.
Noviqu makes it even easier. Preventive maintenance can easily be integrated into the daily, weekly or monthly workflows for employees – and is always at the tip of their fingers. You can schedule any preventive maintenance task on any basis that you’d like so that you keep up with it without having to constantly remember when it should be done – Noviqu can tell you!
Of course, even the most accessible plan might not work unless there’s a reason to do it.
Offer incentives to complete preventive maintenance
It’s important to make sure workers understand the value they bring to the workplace. The simplest way to keep morale up is via recognition – simply acknowledging those who exceed expectations. Reward workers who regularly perform preventive maintenance on their equipment with recognition.
Of course, most workers would appreciate monetary incentives, so instituting programs which reward employees with money or paid time off for consistently maintaining preventive maintenance schedules can go a long way.
It may seem unusual to reward employees for something that’s already part of their job. Failure to complete preventive maintenance can lead to some expensive issues down the road, so it’s worth it to invest early to make sure equipment is maintained and employees take ownership of their work space.
Make maintenance part of the company culture
Initial training goes a long way to instilling important concepts in new hires, but it’s also important to make sure more experienced employees don’t become disenfranchised. If older employees are lax about performing preventive maintenance, newer employees will eventually follow suit.
Managers need to stay on top of preventive maintenance by ensuring employees have enough time to perform it in addition to their regular duties. Make maintenance a priority, and make sure workers know why: maintaining equipment early and regularly keeps it functioning in peak condition.
Investing in the proper resources necessary to establish and maintain a preventive maintenance plan goes a long way towards creating a productive facility. In addition to making sure machines are maintainable, workers have to be engaged and valued. Making sure people are the priority is the key to a successful plan!
More
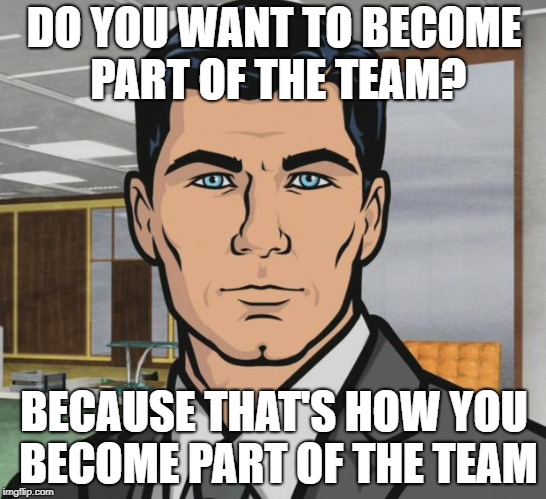
Posted on 7/10/2018 by Anna Haney
Meet Eladio Ballesteros! (Not Pictured)
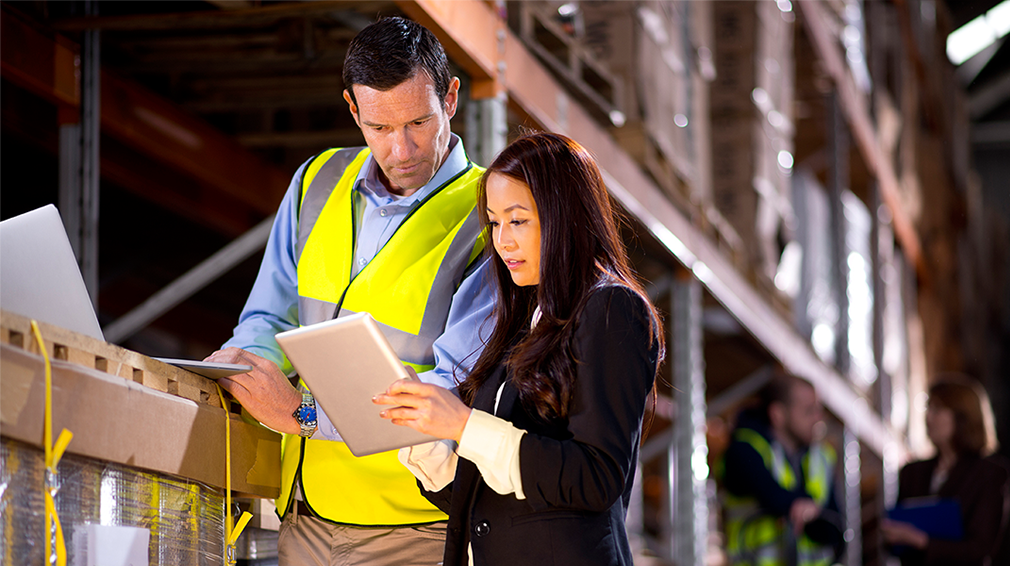
Posted on 06/27/2018 by Anna Haney
Digital reporting can return huge savings on OSHA inspections
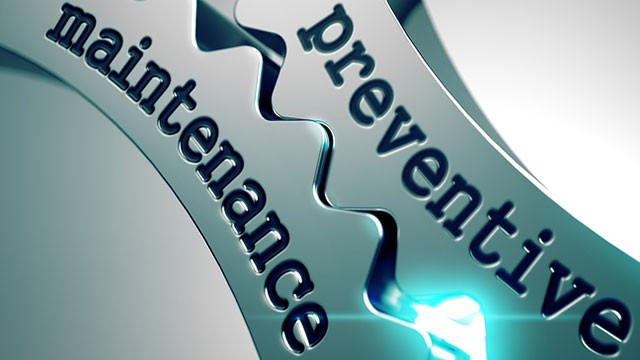
Posted on 08/14/2018 by Allison Opitz