THE NOVIQU BLOG
Safety Incidents in Manufacturing you shouldn't overlook
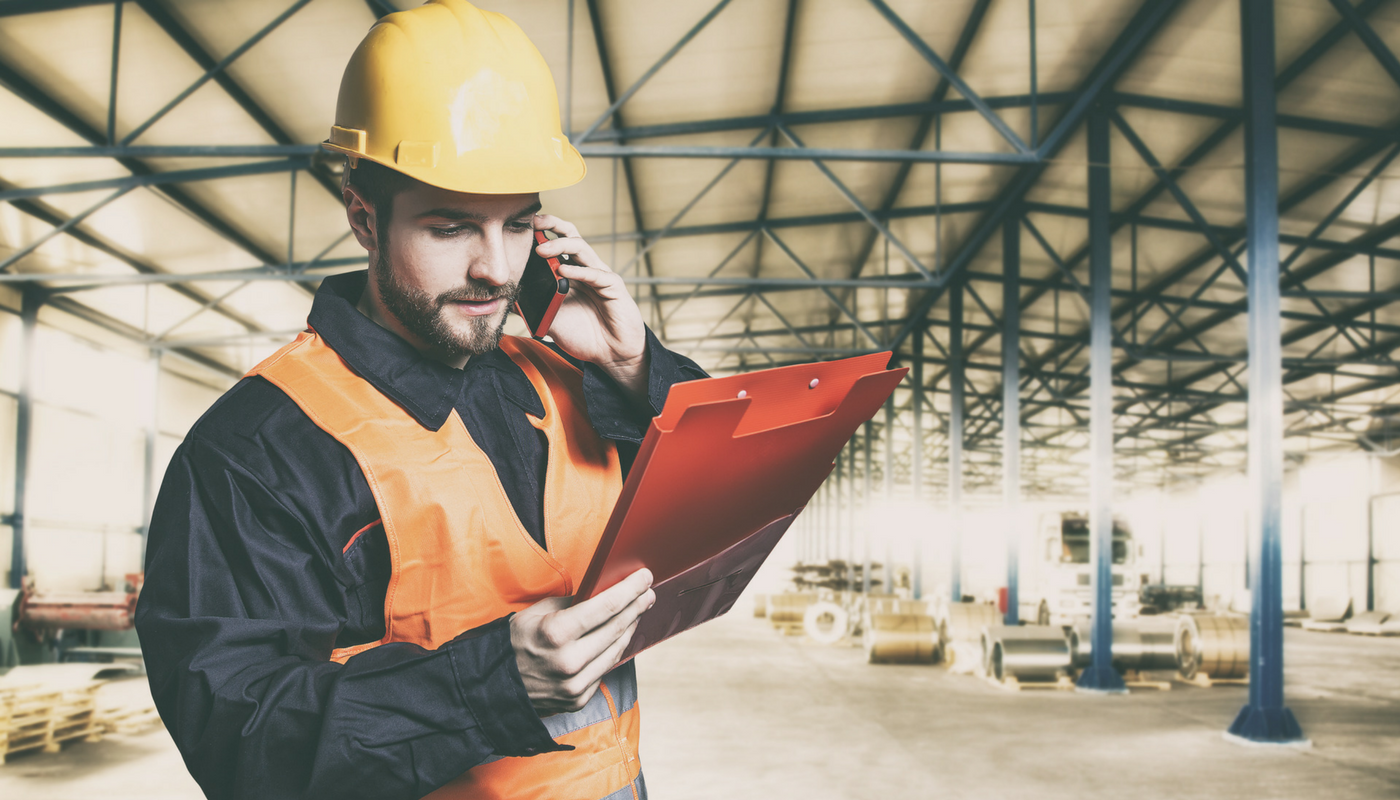
There is no doubt that manufacturing work comes with risks. The nature of the work environment is such that employees are in close proximity to chemicals, large transportation vehicles, complex powerful machinery, and more on a daily basis.
However, the level of risk is not the same for every single task. As we know, the term ‘manufacturing’ is applied to a disparate array of roles particular to the company in question. A plastics manufacturing company will have a different operational structure than a wood processing plant, but the work still falls under the purview of ‘manufacturing’ labor. Indeed, even within a plastics company there are some jobs that come with a much higher risk factor than others.
While it is important for factory safety managers to pay closer attention to the high-risk areas, they cannot do as at the mercy of general safety standards. That means looking at general safety incidents and finding ways to account for them so that menial tasks are as safe as the highly specific tasks on the job. Below are some of the most impactful safety incidents in manufacturing you cannot overlook.
Injuries from Falling Happen All the Time
The most common issue at hand for factory safety standards is incidents of falling. While these incidents are most prevalent in the construction industry, data from OSHA indicates a high rate of falling in manufacturing as well. Studies have shown that falling can be prevented by improving data collection on worker movements and developing more thorough safety protocols around the use of ladders and safety harnesses.
Improper Machine Guarding and the Fallout
Another common source of non-fatal injuries on the job comes from poor machine guarding. OSHA reported on a manufacturer in Green Bay facing nearly $220,000 in penalties after two workers sustained injuries while working on a machinery without adequate safety guards. The takeaway from this incident, is that it’s extremely important to employ more rigorous safety protocols and also improve upon the training program employees are given before using powerful machinery.
Electrical Issues
Electricity is everywhere within manufacturing facilities. A large amount of power needs to be generated on a daily basis to keep the facility running, and the source of this power is electrical. All too often electrical cables slide along the ground, wires become exposed, or a panel remains unlocked for weeks. Then there is the issue of electrical faults which are both dangerous and put a damper on productivity. Maintaining safe electrical protocols such as keeping wiring off of the ground and regularly checking the health of the wiring is imperative to keep your facility running safely and smoothly while minimizing your risk.
Strains, Sprains, or Tears
OSHA data from 2016 shows that relatively benign injuries like strains and sprains were the leading cause of days away from work. Anyone with experience working in the manufacturing sector will understand why such injuries are commonplace. It is important for on-site safety managers to take detailed notes on each case and collect sufficient data to investigate the most common cause of injury. Action needs to be taken to improve problem areas wherever they may lie. If, for example, a number of people have tripped over poorly placed machinery or boxes, then cleanliness standards need to be improved.
Compile Better Data and Your Workplace Will Be Safer
The remedy for these common safety incidents is compiling better workplace data. If you integrate a data management system that can track worker movements and also monitor, in a more accurate way, the operational status of the entire facility, you will be able to isolate and solve problem areas before injuries happen.
More
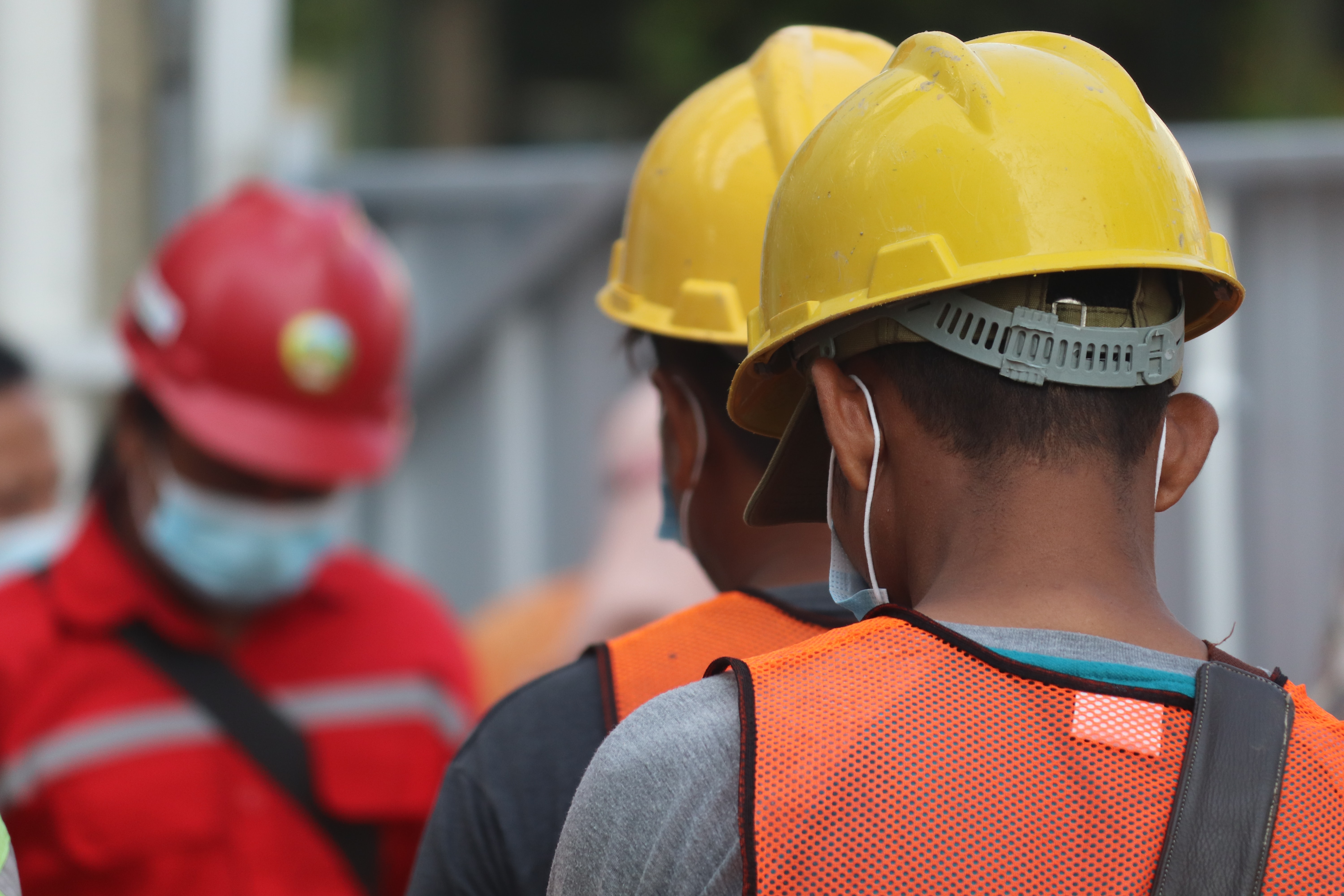
Posted on 03/16/2022 by Anna Haney
Three Steps to Build a Culture Focused on Safety
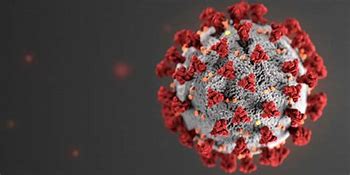
Posted on 03/30/2021 by Anna Haney
Manufacturing in the wake of COVID-19
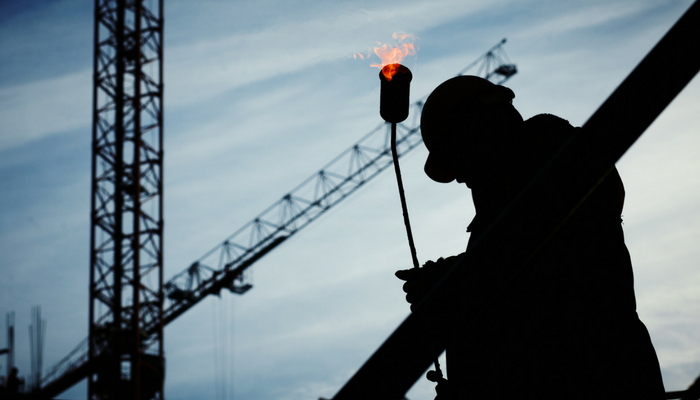
Posted on 01/12/2018