THE NOVIQU BLOG
The Importance of Digital Checklists
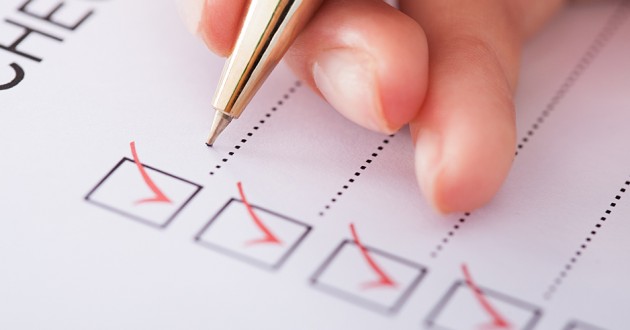
The checklist is an essential tool in any workplace and the manufacturing industry is no different. A proper checklist can help employees – veteran and new – keep up with workplace requirements, procedures, and advancement. Many facilities have checklists for quality assurance, pre-production run, post-production run, training advancement, cleaning, lubricating, and more.
More often than not, these checklists are kept in binders, folders or notebooks, and filled out by hand each time they’re utilized. Checklists are the backbone of how we check accountability, progression and general business practices. Why do we continue to utilize outdated practices for storing and maintaining them?
Why paper sucks
I could just leave it at that: paper sucks and hasn’t been cutting edge since 1899, but it’s so much more than that. The truth is that utilizing paper processes in an ever-changing digital world means losing out on productivity, money, and true insight into your facility.
Paper Costs Money
When it comes to tracking important information in a facility, paper just isn’t sustainable long term. While a single sheet of paper may not be the most expensive thing you’ve contemplated this week, it adds up quickly. (This company spent over $50,000 in hard costs of paper per year before going digital!) The more money spent on paper, the less money spent on truly important functions.
Productivity hits
On average, employees spend 35% of their time at work locating information and documents. Having paper-based processes just adds to the clutter and confusion; not to mention handwriting is not a universally legible thing. Time is wasted each time an employee spends time trying to read the handwriting of another employee, tracking that employee down, or simply searching for the paper in the first place.
Lack of accountability
Paper-based processes provide little opportunity for true accountability between managers and employees. Checklists can be changed on the fly, boxes hastily checked when an inspector comes around, and signatures and dates forged. With a paper list, it’s hard for managers and employees to have true transparency or accountability, which leads to a distrust of the information provided.
Digital beats paper
In a game of rock, paper, digital, digital is the clear-cut winner. (We’re not sure what rock even thought it was doing.) Going digital means increasing efficiencies, decreasing confusion and clutter, and getting better insight into your facility.
Definitive answers
Not using paper means there’s no fudging the numbers, no searching for the right binder, or reading chicken scratch handwriting. When you use the right program – such as Noviqu Ensight – there’s no confusion. You can view every time a checklist has been completed, who completed it and signed off on it, and when. You can even view when a recurring checklist has been missed.
Reporting and metrics
Paper provides no further insight into data. When you go digital, you can see more information about your facility by running reports on how often checklists are completed, who is skipping them, and more. You just can’t get that information without research and time when using a paper system.
It's simply not paper
Digital processes save your facility money and time. In an ever changing, more digital world (hello Industry 4.0), the leaner your production can be the better and this definitely includes trimming down as many paper processes as possible.
Ensight gives insight into your checklists
Noviqu has developed Ensight to provide unique insight into your facility and checklists are a huge part of that. By creating digital checklists, employees and managers alike have a better idea of what’s going on without having to spend time or energy to put the pieces together.
Checklists on your schedule
Do you have a machine that’s supposed to be lubricated once a day? Does it get done? By utilizing our recurring checklists, managers can set checklists to fit the schedule they need. Once a day? Every other week? Once a quarter? No problem. You can even set the max number of occurrences or an end date for the checklist to stop after.
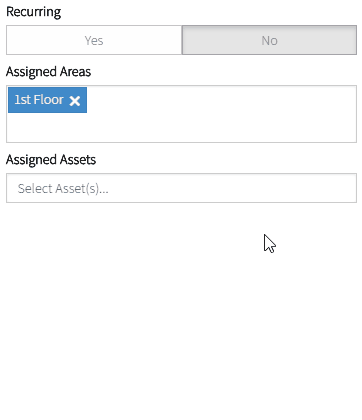
Notifications (in three ways)
When a checklist is due soon, Noviqu will send an alert to any specific manager or role you choose to let them know the deadline approaches. Employees get the choice of receiving in app notifications, browser notifications, emails and text notifications. Our notification system makes sure your employees know when their checklists are due.
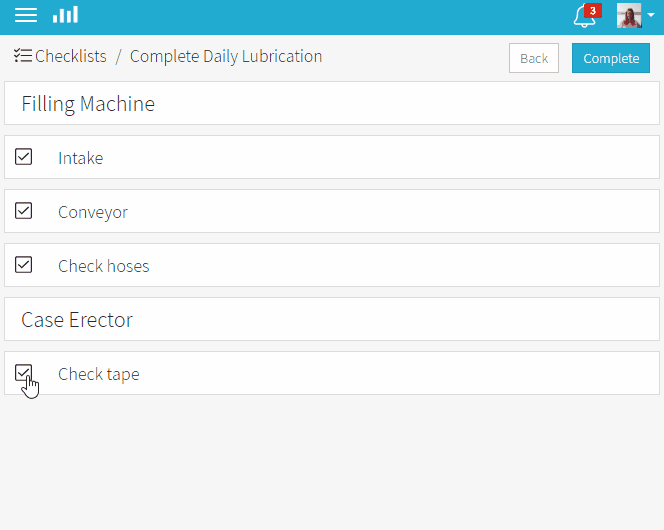
Accountability by signature
Checklists in Noviqu can require the person completing the checklist to sign off on the completed checklist. This records their signature and the date and time of completion so there is no debate on when it happened. As a bonus, you can require a second user – such as a manager or trainer – to sign off on the completion as well.
Flexibility and better information
Because Noviqu’s checklists are built to handle any kind of flow you need them to, your checklists are only limited by what you can think up. Some examples of popular checklists include:
- Quality Assurance
- Inspections
- Machine Testing
- Pre or Post Production Runs
- Safety Inspections
- And more!
By utilizing Noviqu’s system, the information presented in a checklist can be used to run reports again safety information, training logs, or maintenance records.
Noviqu Ensight is a platform made for keeping employees engaged, information in one place and at the user’s fingertips when they need it most, and giving managers and users better transparency, and checklists are just one way we do it. If you’re interested in learning more about Noviqu, our checklist system, or about how we can help you become more efficient, contact us today!
More
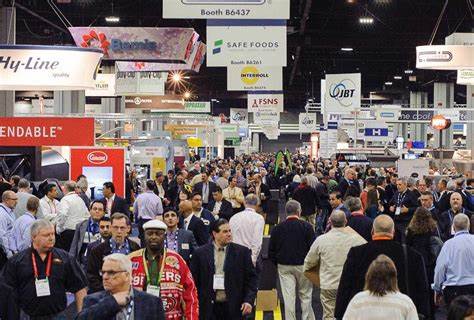
Posted on 02/02/2022 by Chad Haney
We attended the International Production and Processing Expo; Here are our Thoughts
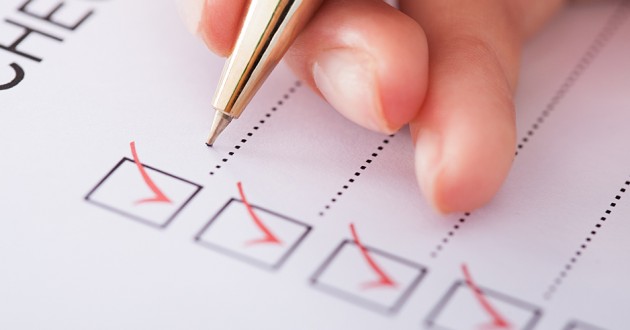
Posted on 06/06/2018 by Anna Haney
The Importance of Digital Checklists
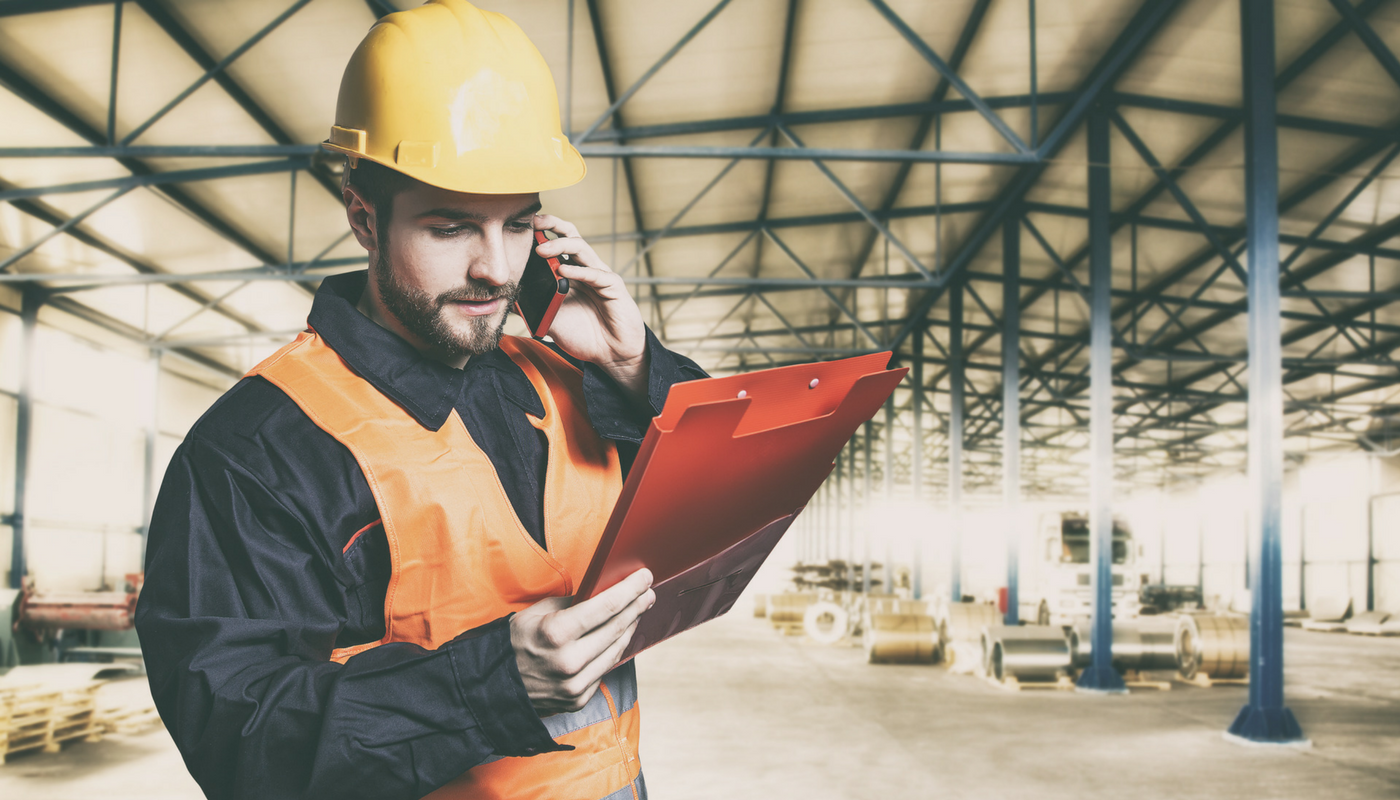
Posted on 03/13/2018