THE NOVIQU BLOG
Should I care about Lean Six Sigma?
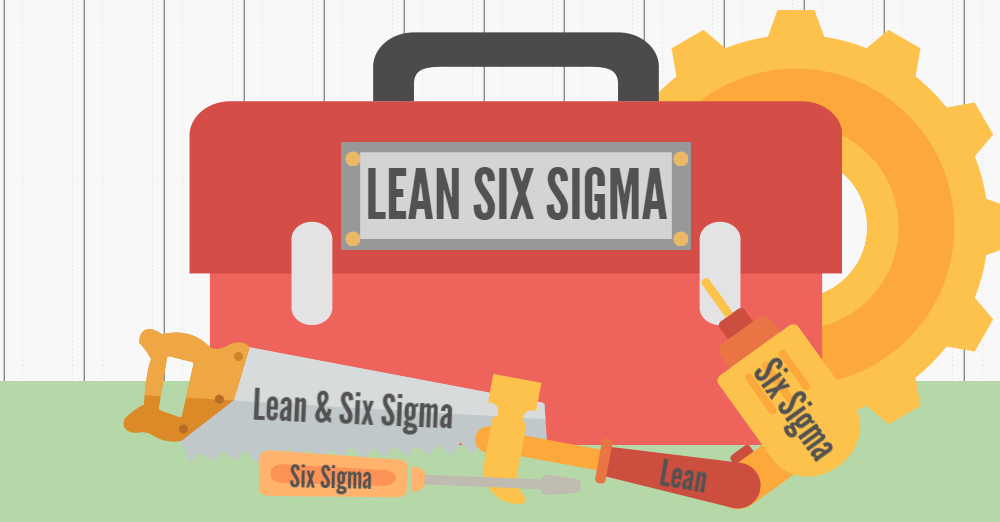
To the regular worker, Lean Six Sigma (LSS) is a collection of abstract words that upper management unleashes upon the workforce to cause headaches in the name of efficiency. To management, LSS is a concept that they think their facility needs to implement, but they may not know much more than that. What exactly is LSS, and what does it actually mean to an organization, in the real world – and should you care?
What is Lean Six Sigma?
LSS is certainly an abstract concept, but this concept is designed to help project managers run more profitable and efficient businesses. It’s a combination of two separate ideologies: Lean and Six Sigma, which are two different but related frameworks companies use to improve process efficiency and save money.
Lean is a project management tool to reduce waste in manufacturing. It’s designed to help businesses look at processes from the bottom-up to find and eliminate waste. Six Sigma, on the other hand, is a tool to reduce variation in those processes. They accomplish similar goals and, when combined and executed properly, claim to transform your facility into its most efficient, profitable form.
Why Should I Care About Lean Six Sigma?
Chances are, if you’re thinking about LSS, you have some processes in your facility or business that need improvement, whether that’s to reduce waste, increase output, or reduce variation. LSS is unique in that instead of trying to solve every problem your facility may have, management devotes a highly-trained portion of the workforce to work one specific problem, always with the goal of reducing or eliminating waste.
Upper management certainly cares about high-level priorities such as reducing waste and saving money, but workers need to have buy-in for the LSS recommendations to work long-term. Workers should have input on identifying areas that need improvement, and management needs to listen. Management also needs to be sensitive to workers’ concerns that changing processes might result in more work, oversight, or may not make sense right away. Emphasize that less waste means a more stable and positive company.
Once the workforce has been given an opportunity to contribute, a problem statement needs to be created so the project has clear definition. But the problem statement only goes so far: without serious commitment from management and the workforce, the LSS process won’t yield any fruitful solutions.
Every LSS project is different, just as every facility is different. LSS simply provides a framework for coming up with solutions to improve your own processes and does not seek to provide a one-size-fits-all solution.
Streamline Your Processes With Noviqu
Only you can decide whether LSS is right for your business. While it can help create solutions to reduce waste and variation, it only works with long-term commitment from upper management and a highly engaged workforce. There are many tools available to transform your processes to create a profitable, efficient facility.
A common source of waste in facilities today is monitoring metrics, managing documentation, and keeping up with maintenance. Implementing an enterprise content management system like Noviqu can help eliminate wasted time and resources spent on keeping paper or digitally-disorganized records, and can also provide valuable insights into existing processes in real time – without needing to spend months on an LSS project.
More
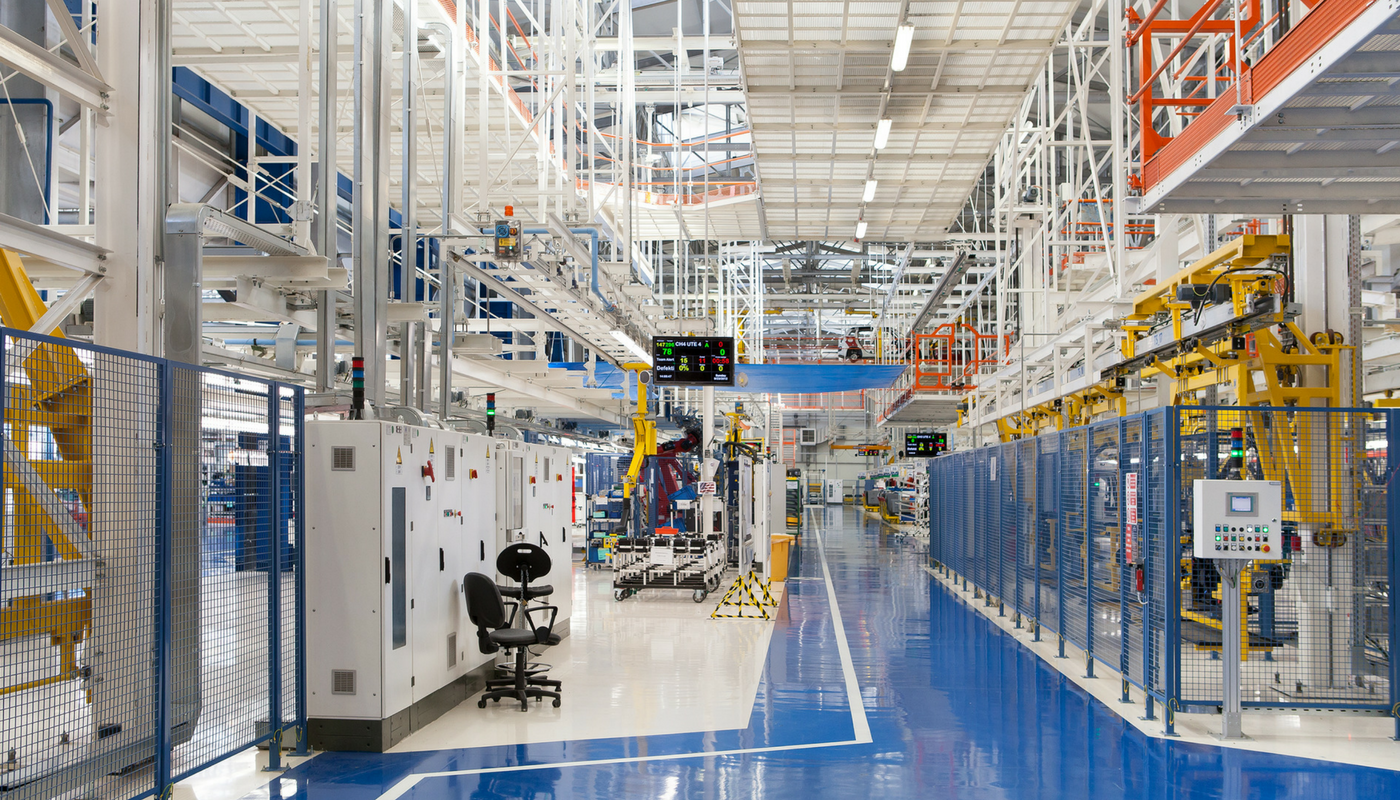
Posted on 04/10/2018
Four Principles for Keeping your Warehouse Clean and Organized
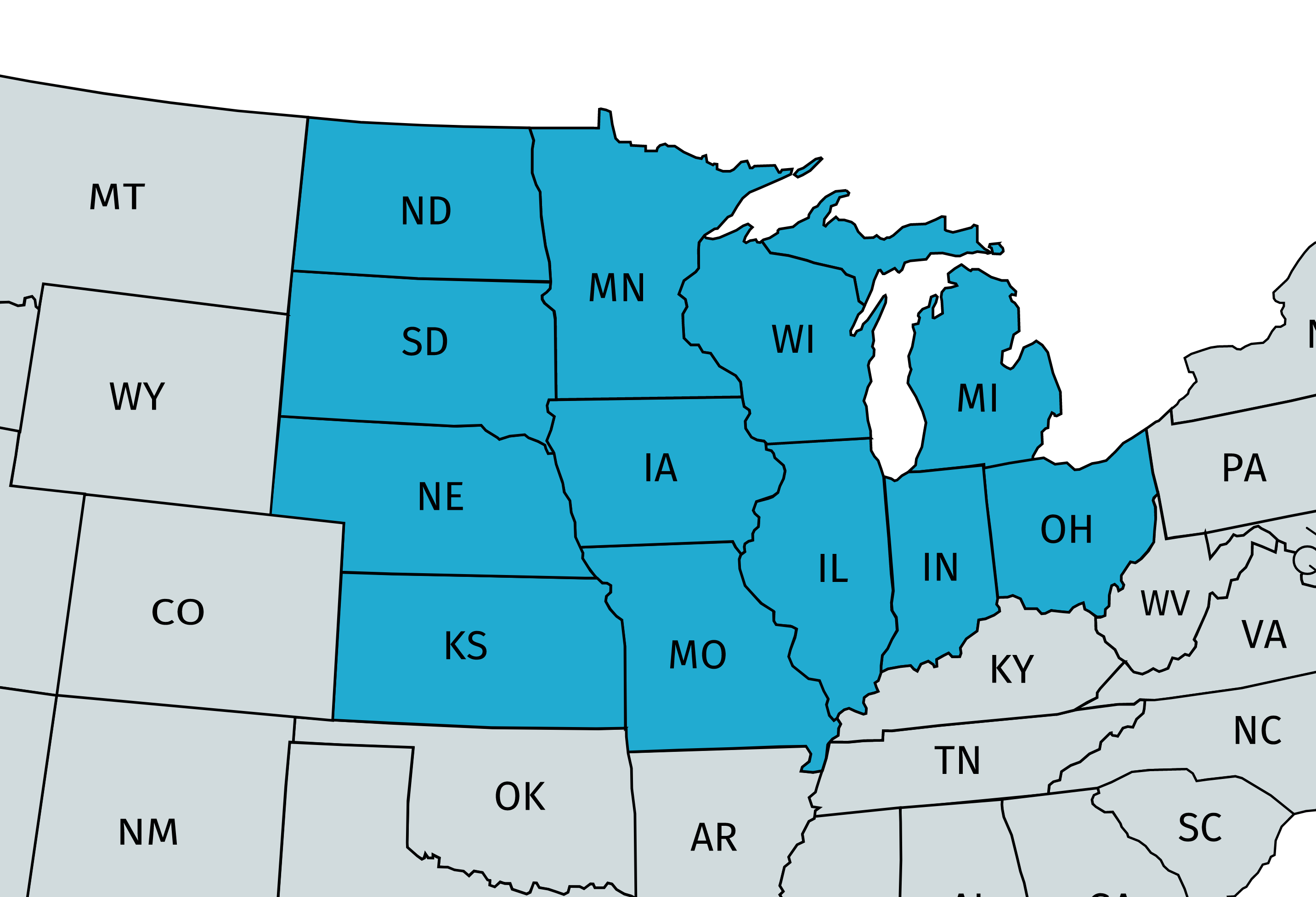
Posted on 07/09/2018 by Anna Haney
Manufacturing isn't dead; Come to the Midwest
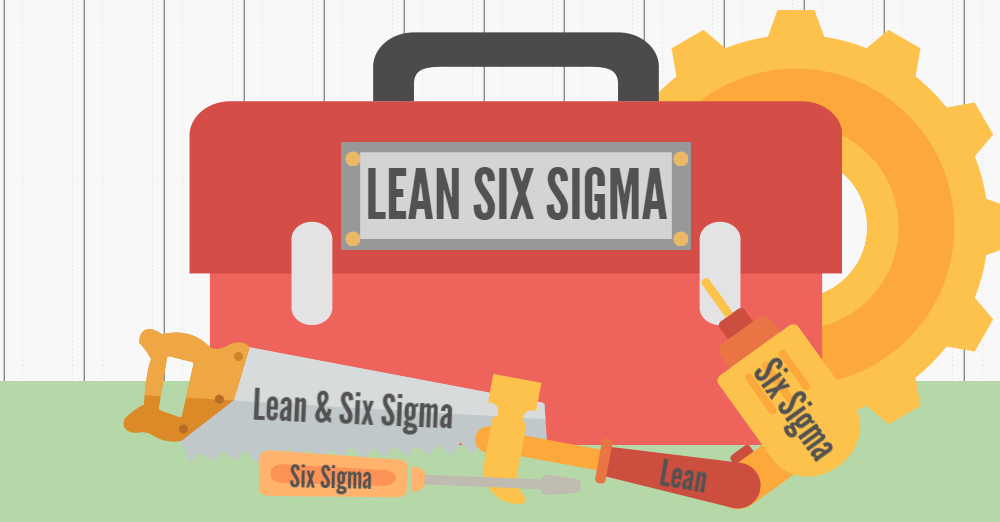
Posted on 12/05/2018 by Allison Opitz